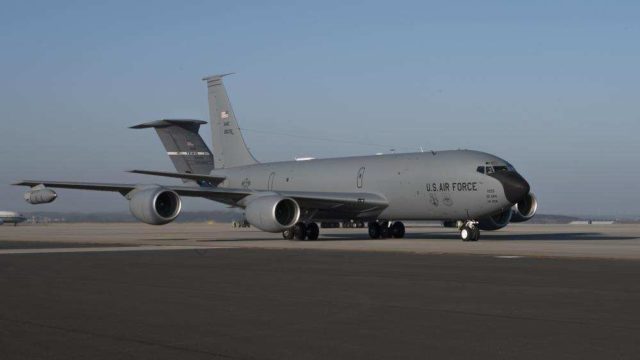
The 2-pound part that nearly sent a KC-135R Stratotanker to the scrapyard KC-135 Stratotankers arrive for European Theater support (U.S. Air Force/Released)
Fully loaded with fuel, the KC-135R Stratotankers at the Nebraska Air National Guard Base can take off weighing more than 320,000 pounds and stay in the air for hours.
But one of them was recently grounded — and nearly sent to the scrapyard — by a broken, 2-pound piece of aluminum called a rudder snubber support fitting.
The base’s hydraulic crew discovered a crack and a misshapen bolt hole in the part while repairing a nearby leak late last year.
“They were looking at different hydraulic systems,” said Master Sgt. James Kenning, who runs the base’s Aircraft Metals Technology Shop. “And as they were cleaning up the hydraulic fluid, they noticed it was broken.”
The shoehorn-shaped part — about 3 inches wide and 8 inches long — is critical to the aircraft. It serves a role similar to a car’s shock absorber mount, but on a larger, and more important scale, helping to stop the jet’s rudder from vibrating in flight.
Kenning and his three-person crew couldn’t just order a replacement; the part was forged for this Stratotanker more than 60 years ago, and there was no surplus supply of rudder snubbers.
“This aircraft has been asked to fly a lot longer as originally planned. It was never meant to be in the Air Force this long.”
The 155th’s planes are flying gas stations, providing in-flight refueling to U.S. military planes around the world. When not deployed, their pilots train extensively, so the jets log ample flying time. But all eight planes were built in the early 1960s, so they’re past their prime.
Which means his shop had been here before, asked to replicate an aircraft part that was no longer available. But members of his crew typically relied on drawings from the late 1950s, when the jets were introduced. They could follow directions, even if they were sometimes hand-sketched.
In this case, though, nobody had expected this part to fail, so there were no specs.
And the stakes were high, Kenning said: “When this is broke, the plane is not allowed to fly. If we can’t re-create this, the plane is scrapped.”
In mid-January, his shop earned approval from Air Force engineers to do something it had never done before: Reverse-engineer a component from scratch, using only the broken part as a guide for building its replacement.
The process would take time, technology, patience — and a special order of high-strength aluminum.
Kenning started with a 3D scanner, measuring the failed fitting from all angles, scanning one side, then flipping it over to scan another. He spent nearly three weeks on that, staring at his monitor, cleaning up the data.
Then he printed a plastic prototype with a 3D printer. But it wasn’t quite right, so he and his crew made some changes, and printed another.
The material was almost a problem. Engineers at Tinker Air Force Base near Oklahoma City had approved the use of two types of aircraft-grade aluminum, so Kenning started working the phone.
“I called five different large companies to try to track down either kind. We were starting to get scared.”
He finally found a company willing to mix up a special batch, and ordered a 4-inch-square, 3 1/2-foot long loaf, or billet — enough aluminum for four rudder snubber support fitting attempts.
That was insurance, Kenning said. When you’re making one-off parts, the first try often doesn’t work.
But after 26 hours on the CNC machine — and then an ultrasound to look for irregularities — this one did work.
And late last month, his crew’s efforts were recognized by the chief of the National Guard Bureau. But more importantly, it put the 60-year-old Stratotanker back in the air, Kenning said.
“It hasn’t fallen out of the sky yet. We essentially brought it back from the dead.”
___
(c) 2022 Lincoln Journal Star Distributed by Tribune Content Agency, LLC